Understanding the Challenges of Filling Machines in Global Supply Chains
In today's interconnected world, global supply chains are more complex than ever, and they face various challenges that can disrupt productivity and efficiency. One critical component of these supply chains is the technology used in manufacturing and packaging processes; among these, filling machines play a pivotal role. These machines are essential for accurately and efficiently dispensing products across various industries, from food and beverages to pharmaceuticals. However, as businesses strive to meet increasing consumer demands, the challenges associated with filling machines have come to the forefront, highlighting the need for innovation and adaptation in manufacturing practices.
Navigating the obstacles posed by filling machines requires a deep understanding of their operational capabilities as well as the limitations that can arise due to factors such as supply chain disruptions, equipment maintenance, and technological advancements. As companies expand their reach in the global marketplace, they must consider how to best integrate filling machines into their production lines while ensuring reliability and consistency. This blog will delve into the intricacies of filling machines within global supply chains, exploring the challenges they face and the solutions that can help businesses thrive in an ever-evolving landscape.
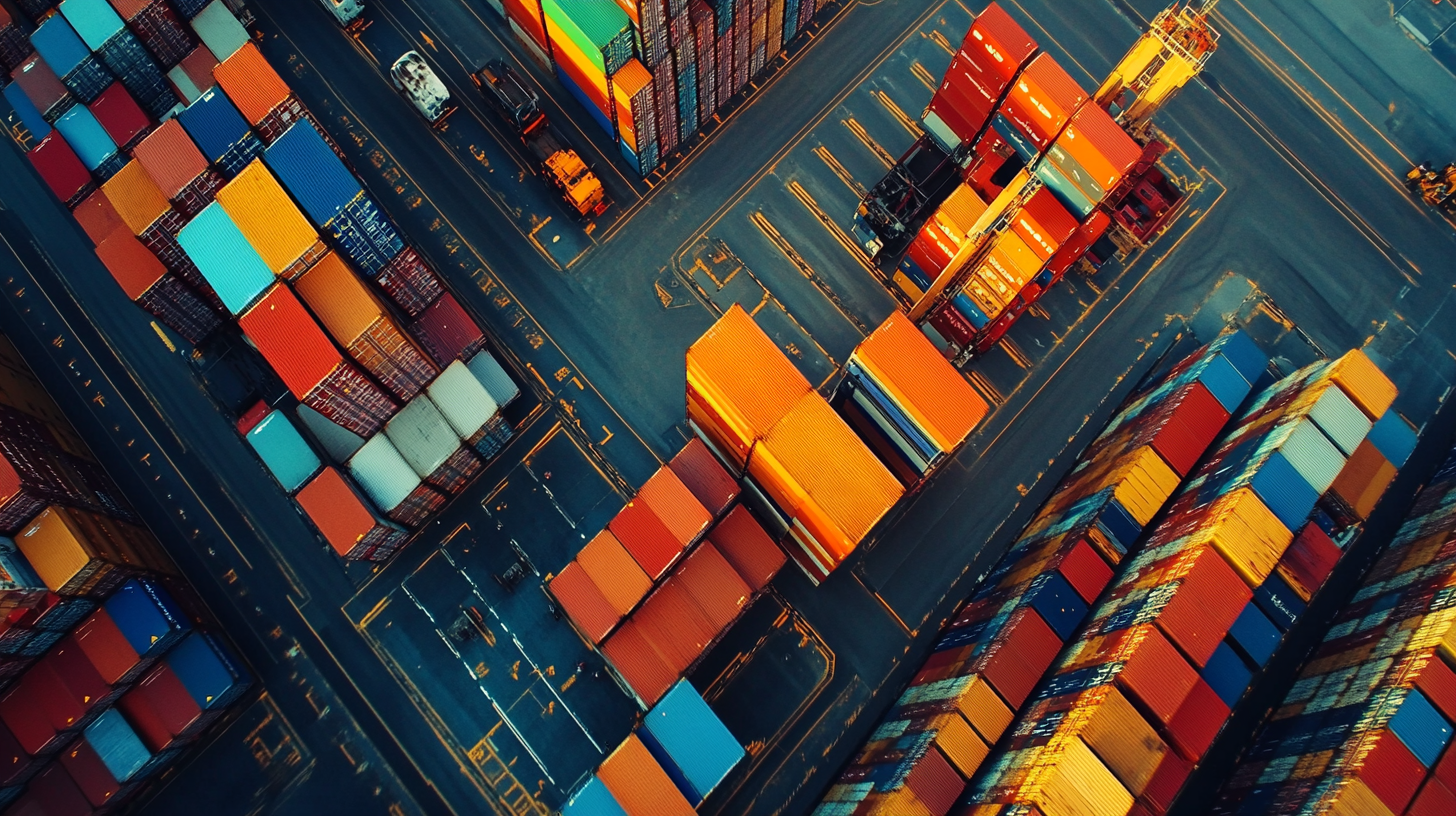
Challenges in Sourcing Reliable Filling Equipment for Global Operations
Sourcing reliable filling equipment for global operations presents a unique set of challenges that can significantly impact the efficiency and productivity of manufacturing processes. One major challenge is the variability in equipment specifications and standards across different regions. Manufacturers must navigate diverse regulations and compliance requirements, which can complicate the procurement of suitable filling machines. Vendors may offer equipment that meets local standards but falls short of international requirements, leading to potential delays and increased costs in supply chain management. Additionally, the logistics of transporting filling equipment across borders can introduce significant complications. Shipping delays, customs regulations, and transportation costs can all contribute to the extended lead times that companies experience when sourcing machinery from international suppliers. This can have a knock-on effect on production schedules, causing ripple effects throughout the supply chain. Moreover, ensuring consistent quality in filling machinery from various suppliers is essential for maintaining production efficiency. Businesses need to conduct thorough due diligence and establish strong relationships with reliable suppliers. This often requires investing time in audits and quality checks to ensure that the equipment will perform reliably across different sites, adding another layer of complexity to the sourcing process. Hence, companies must approach equipment sourcing with a strategic mindset, considering not only the immediate purchase but also the long-term implications for global operations.
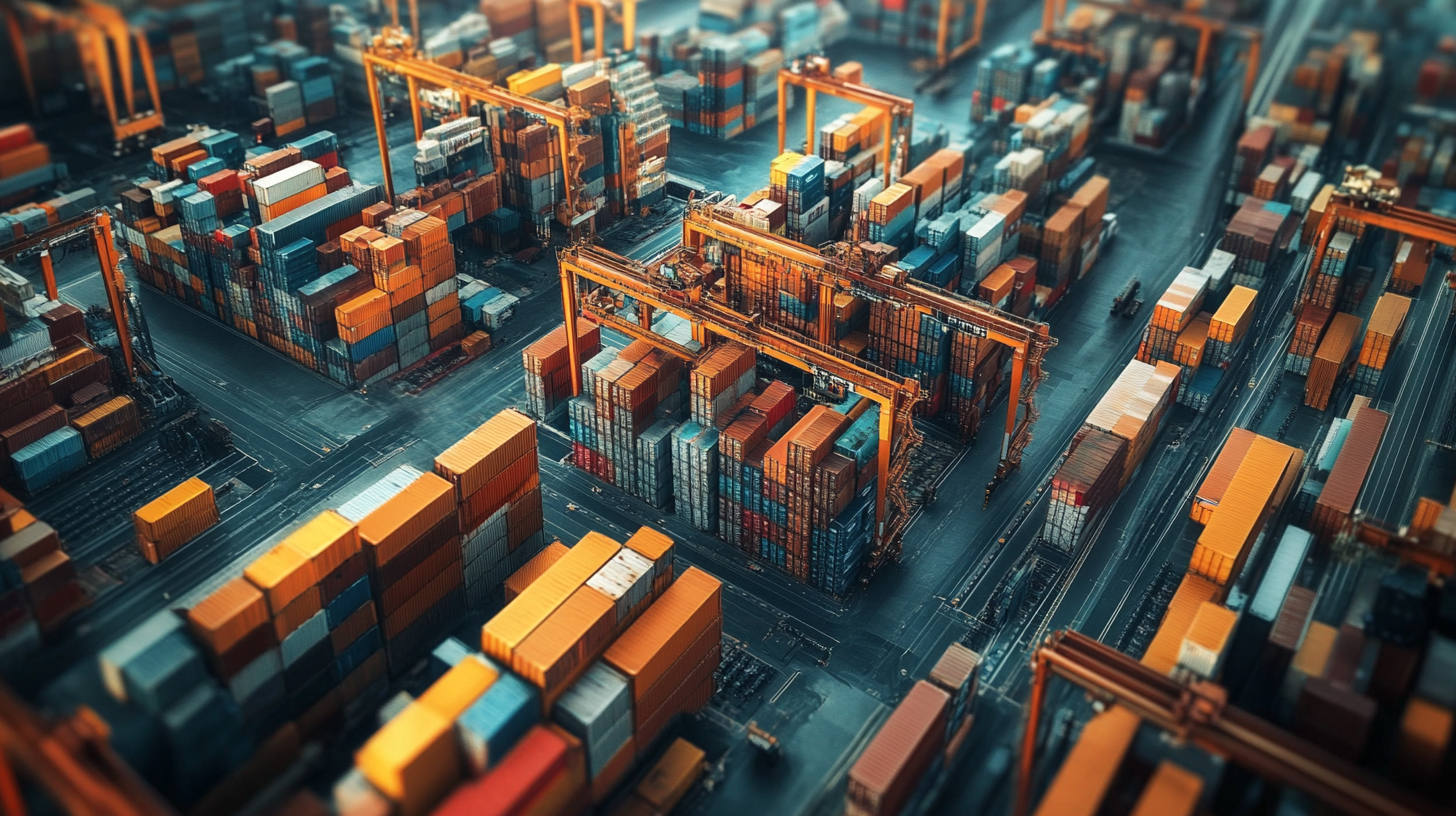
Impact of Supply Chain Disruptions on Filling Machine Availability
The recent disruptions in global supply chains have significantly impacted the availability of filling machines, a crucial component in various industries from pharmaceuticals to food and beverage. According to a report by McKinsey & Company, 75% of companies have reported supply chain interruptions due to factors such as the COVID-19 pandemic, geopolitical tensions, and transportation bottlenecks. These challenges have created a ripple effect, delaying production timelines and increasing costs, which in turn has strained the filling machine market.
Filling machines, which account for a significant portion of production line efficiency, have seen demand outstrip supply as companies scramble to meet heightened consumer needs. The Freedonia Group estimates that the global market for filling machines will reach $5.5 billion by 2026, with a compound annual growth rate (CAGR) of 3.8%. However, manufacturers are facing shortages of key components like sensors and control systems, leading to extended lead times for new installations and repairs. Reports indicate that some manufacturers are experiencing delays of up to six months, severely impacting operational capabilities.
Moreover, the increasing complexity of modern filling machines, which often integrate advanced robotics and IoT technology, adds another layer of difficulty in sourcing parts and ensuring maintenance. Industry experts suggest that companies need to rethink their supply chain strategies to enhance resilience, including diversifying suppliers and investing in local production capabilities. As businesses navigate these challenges, understanding the direct correlation between supply chain disruptions and the availability of filling machines becomes paramount for strategic planning and operational continuity.
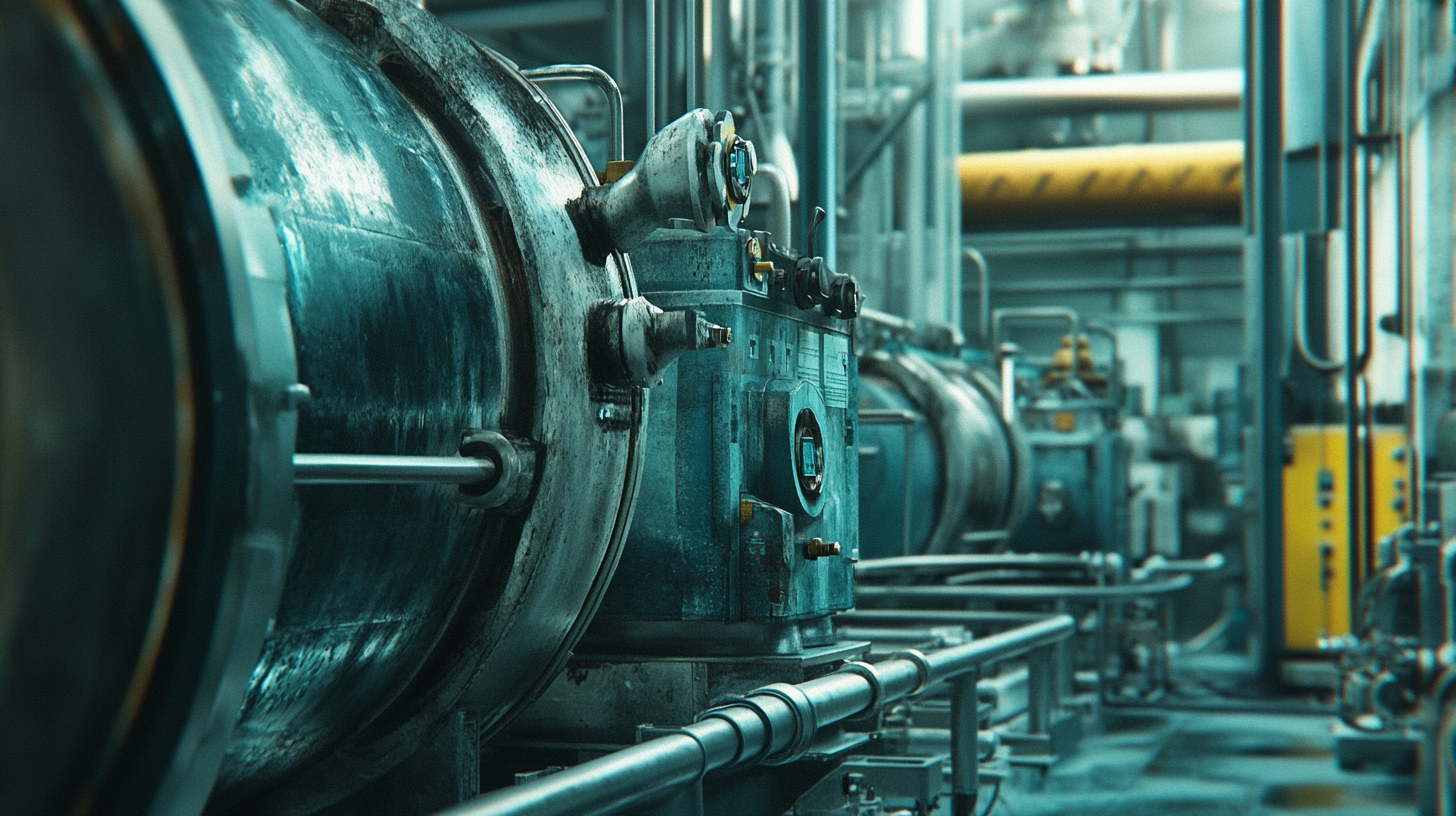
Technological Innovations Addressing Filling Machine Inefficiencies
In the fast-paced environment of global supply chains, filling machines are often at the forefront of productivity challenges. These machines, crucial for packaging liquids and other materials, face inefficiencies that can ripple throughout the supply chain. However, technological innovations are emerging to address these pressing issues, ensuring that businesses can maintain their competitive edge.
Recent advancements in automation technology have significantly improved the performance of filling machines. Smart sensors and IoT integration allow for real-time monitoring and adjustments, reducing downtime and enhancing accuracy. These systems can predict maintenance needs before breakdowns occur, minimizing disruptions and ensuring a more fluid production process. Further, machine learning algorithms are enabling filling machines to adapt to various product types and levels of viscosity, which helps streamline the filling process and reduces waste.
Moreover, the introduction of advanced robotics and AI-powered systems has transformed traditional filling operations. These innovations not only speed up the filling process but also ensure consistency and precision that manual processes cannot achieve. As companies continue to seek ways to optimize their supply chains, investing in these technological solutions will play a pivotal role in overcoming the inefficiencies that have historically plagued filling operations. By embracing the latest advancements, businesses can position themselves for success in a rapidly evolving market.
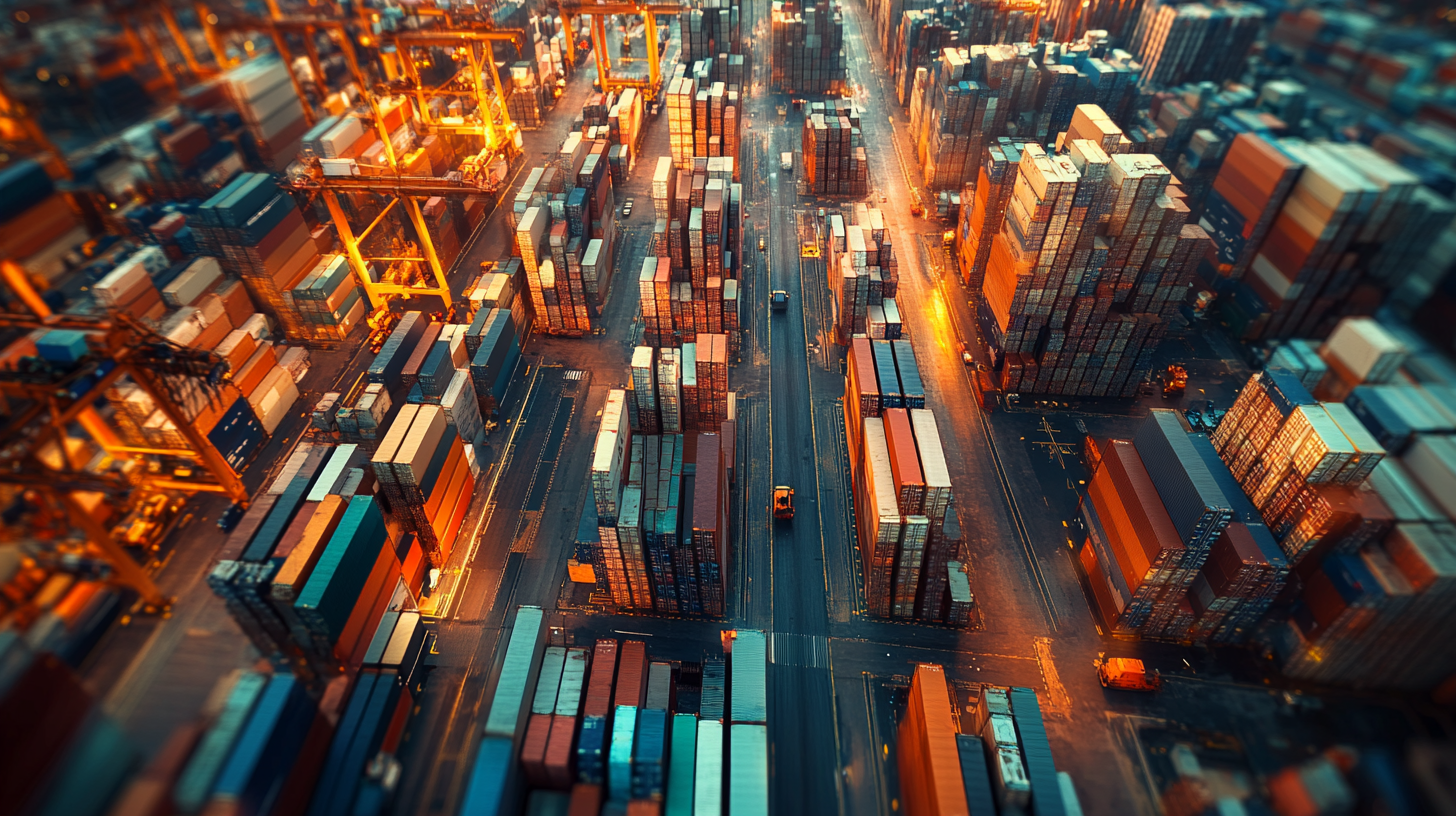
Regulatory Compliance and Its Effects on Filling Machine Operations
In today’s global supply chains, filling machines are pivotal in ensuring efficient production and packaging. However, their operation is heavily influenced by various regulatory compliance standards that differ by region. Companies must navigate an intricate web of regulations, which can vary significantly depending on the market, product type, and local governance. This necessitates not only a deep understanding of the regulations but also a proactive approach to adapt filling machine operations accordingly.
One major regulatory consideration is the adherence to sanitary and safety standards, particularly in industries like pharmaceuticals and food and beverage. Non-compliance can lead to severe repercussions, including product recalls, fines, and damage to a brand’s reputation. Filling machines must be designed and operated in ways that comply with these regulations, which often means regular logging of operations, maintenance checks, and updated training for operators to ensure they are well-versed in compliance requirements. As such, the need for flexible and easily adjustable filling machines is paramount in addressing the evolving compliance landscape.
Furthermore, navigating international regulatory frameworks can present additional challenges, especially for companies looking to penetrate new markets. Each territory may enforce distinct compliance protocols, which require filling machines to be not only versatile but also capable of being modified to meet various standards seamlessly. Companies must integrate compliance checks into their operational processes and invest in technologies that allow for easy calibration and verification. By aligning their filling machine operations with regulatory demands, businesses can enhance their supply chain resilience and ensure smoother market access.
Strategies for Overcoming Filling Machine Challenges in Global Markets
Global supply chains face a myriad of challenges, and filling machines play a crucial role in maintaining efficiency and quality. To tackle the complexities associated with filling machines in diverse markets, businesses must adopt strategic approaches. One effective strategy is the implementation of advanced automation technologies. By integrating state-of-the-art filling machines equipped with smart sensors and real-time monitoring systems, companies can greatly enhance their operational efficiency and reduce downtime. This technology not only streamlines production processes but also adapts seamlessly to varying products and packaging requirements across different regions.
Furthermore, fostering robust communication within the supply chain is vital. Establishing clear lines of communication between manufacturers, suppliers, and distributors ensures that potential issues with filling machines are identified and resolved quickly. Regular training sessions and updated guidelines for operators can mitigate human error, contributing to smoother operations. Additionally, cultivating partnerships with local suppliers can alleviate logistics challenges, making sourcing parts for filling machines more efficient and cost-effective.
Lastly, embracing a proactive maintenance culture is essential for sustaining the performance of filling machines. By scheduling regular maintenance checks and utilizing predictive maintenance techniques, businesses can prevent unexpected breakdowns that disrupt supply chains. This focus on maintenance not only prolongs the lifespan of equipment but also ensures that filling operations remain consistent and reliable, ultimately leading to greater customer satisfaction and loyalty in competitive global markets.