Innovative Approaches for Mastering Tray Sealing Technology
In the fast-evolving food packaging industry, mastering tray sealing technology has become crucial for manufacturers aiming to enhance efficiency, reduce waste, and meet consumer demands for convenience. According to a recent report by MarketsandMarkets, the global tray sealing machine market is projected to reach USD 4.25 billion by 2026, growing at a CAGR of 6.2% from 2021. This trend underscores the increasing reliance on innovative packaging solutions within the food sector, where shelf life, food safety, and consumer appeal are paramount.
Furthermore, advancements in tray sealing machine technology are enabling producers to achieve better product integrity and sustainability. With the rising consumer trend toward fresh and convenient meal options, efficient sealing processes ensure that products remain uncontaminated and retain their freshness longer. Manufacturers are now exploring cutting-edge methods, including automation and smart technology integrations, to optimize their operations. This blog will delve into progressive strategies for mastering tray sealing technology, highlighting how industry leaders are navigating challenges and leveraging innovations to stay competitive in a dynamic market.
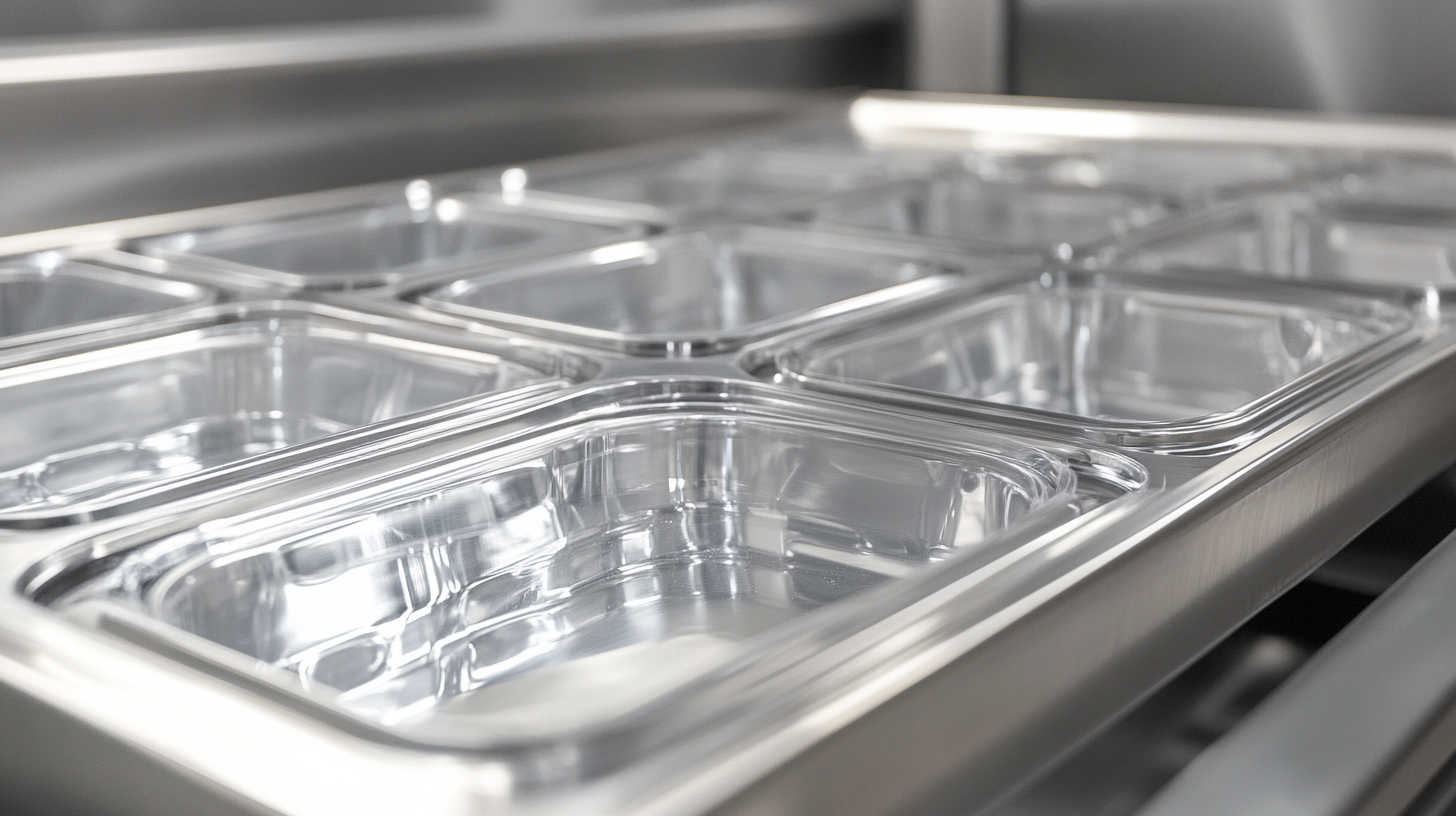
Emerging Trends in Tray Sealing Techniques for Enhanced Food Preservation
The landscape of food preservation is undergoing a revolution, particularly in the realm of tray sealing technologies. As the global vacuum packaging market is projected to grow from $32.91 billion in 2025 to an impressive $50.04 billion by 2032, the need for innovative approaches in food packaging becomes increasingly critical. Among the emerging trends, Modified Atmosphere Packaging (MAP) shines as a frontrunner, enhancing the longevity and safety of perishable products by drastically reducing oxygen levels and thereby slowing spoilage. Recent advancements in materials science have brought plant-based edible films and coatings to the forefront as sustainable alternatives for food packaging. These innovative solutions not only contribute to enhanced food preservation but are also in alignment with the growing consumer demand for environmentally friendly packaging options. The U.S. food vacuum sealers market, anticipated to reach $3.45 billion by 2029, highlights the shifting consumer preferences towards vacuum-sealed solutions that maintain freshness and extend shelf life. Furthermore, techniques such as High-Pressure Processing (HPP) are gaining traction within the industry, offering effective methods for microbial control without the detrimental effects of high heat. As the food sector pivots towards more sustainable practices, integrating these high-tech sealing and packaging methods is essential for meeting the challenges posed by rising food waste and the demand for high-quality preserved foods. With these trends shaping the future of food safety and preservation, it's clear that the evolution of tray sealing technology is not merely a response to market demand, but a vital step towards a sustainable and efficient food supply chain.
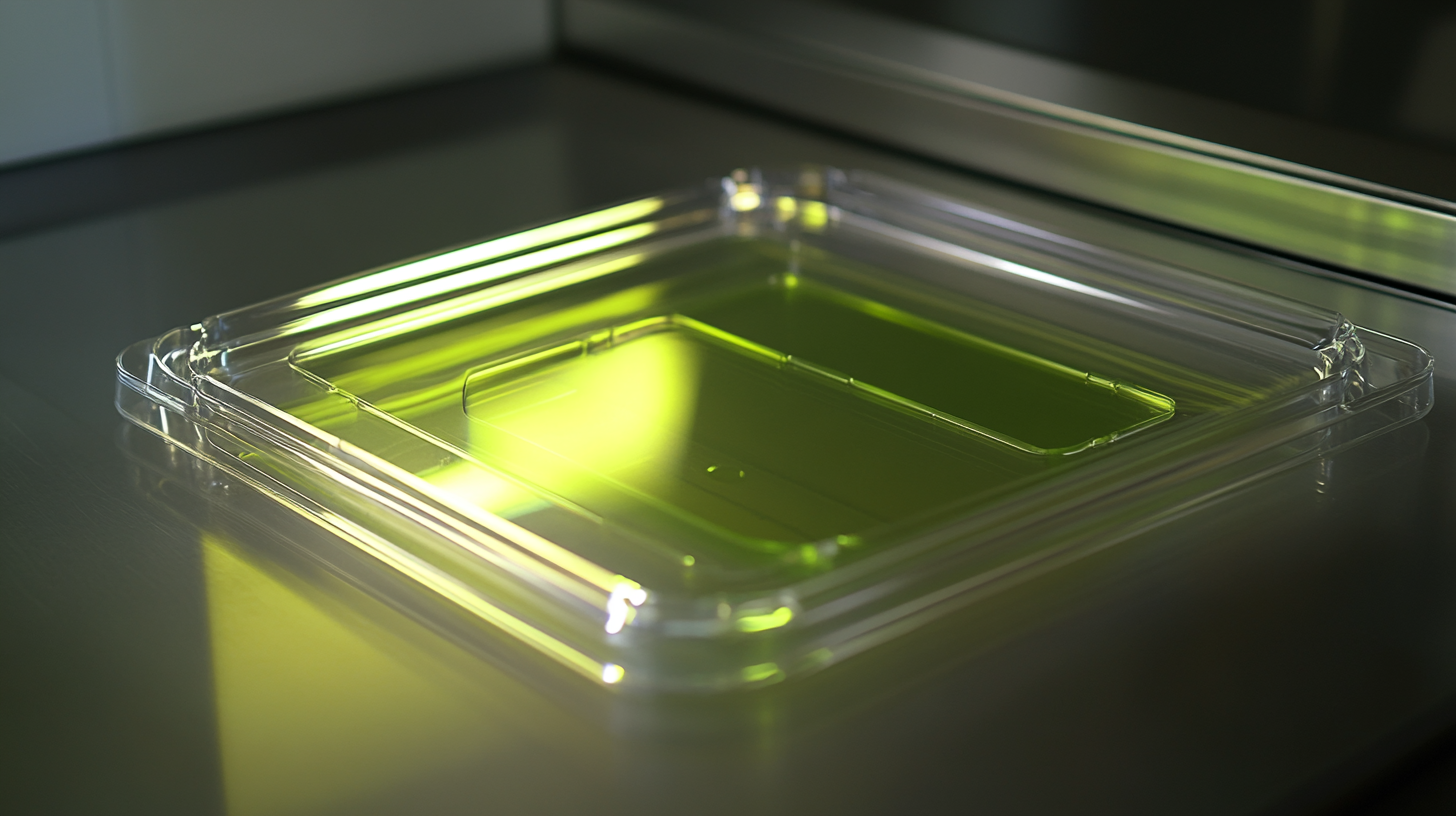
The Role of Automation in Streamlining Tray Sealing Processes
The advancement of automation has played a pivotal role in revolutionizing tray sealing technology. As industries strive for efficiency and precision, automated systems have emerged as essential components in streamlining tray sealing processes. Automation not only enhances the speed of production but also increases consistency and reduces the likelihood of human error, enabling manufacturers to meet rising consumer demands with ease.
Integrating automated machinery into tray sealing operations facilitates a seamless workflow. Automated sealing machines can quickly adapt to various tray formats and materials, ensuring that products are sealed securely and efficiently. This flexibility allows manufacturers to introduce new products to the market without incurring significant downtime or additional labor costs. Additionally, real-time monitoring and data analytics enable operators to gather insights on production performance, allowing for continuous improvement and optimization of sealing processes.
Beyond efficiency and adaptability, automation also enhances food safety and compliance. With stringent regulations governing packaging and food preservation, automated tray sealing systems can be equipped with advanced sensors to detect issues such as improper sealing or contamination. This proactive approach not only protects the quality of the product but also instills consumer confidence in brand integrity, ultimately driving sales and customer satisfaction.
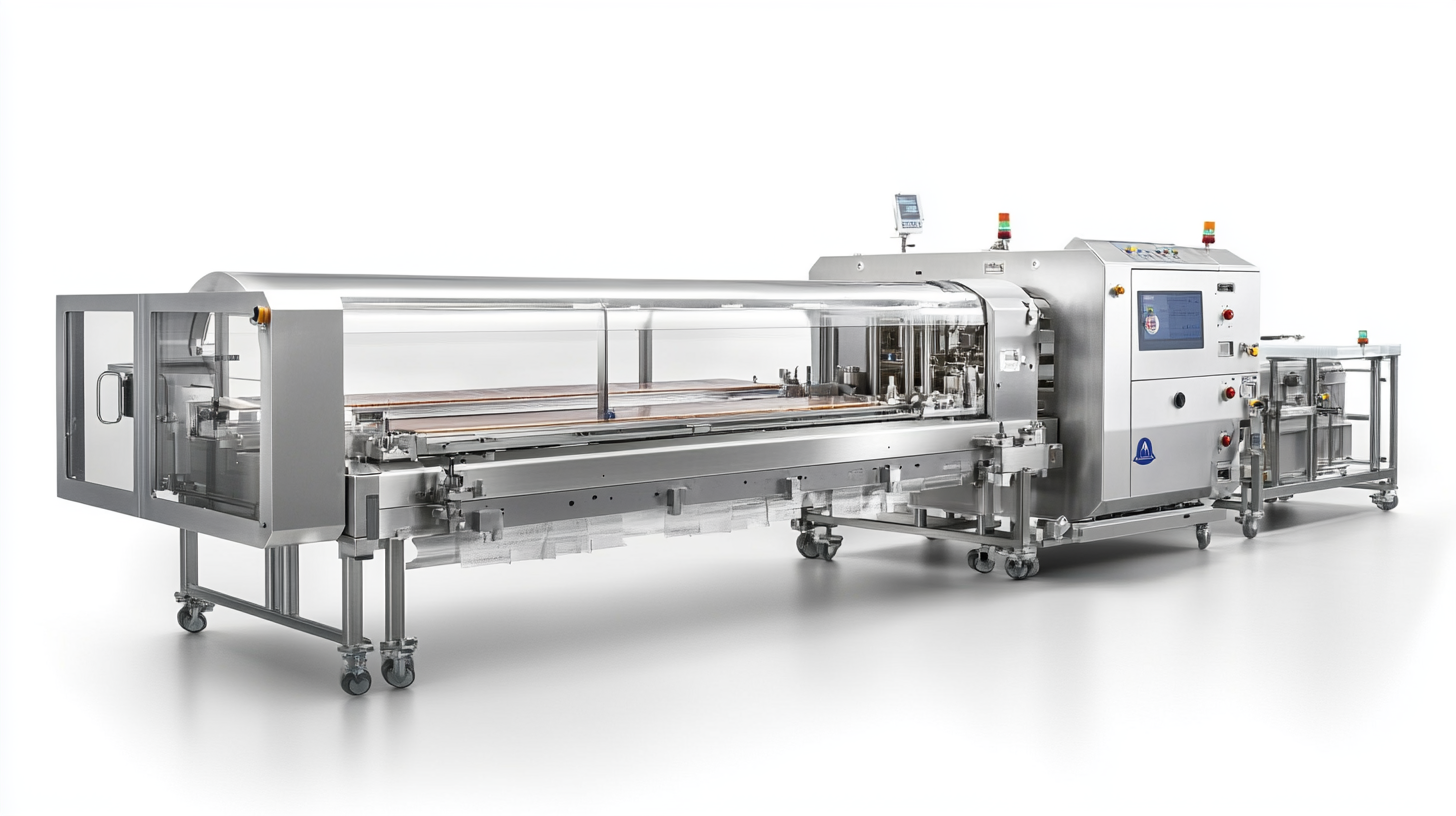
Sustainable Materials in Tray Sealing: Innovations and Benefits
Sustainable materials are at the forefront of innovations in tray sealing technology, revolutionizing the packaging industry. Recent trends highlight a growing commitment to environmental responsibility, with numerous companies unveiling eco-friendly lidding films and tray solutions designed to reduce waste and enhance recyclability. For instance, the latest lidding innovations focus on extending the shelf life of fresh produce, meat, and dairy products, minimizing food spoilage and maximizing sustainable practices within packaging. A significant aspect of this shift is the increasing consumer demand for sustainable packaging options, driving companies to innovate and adapt to eco-conscious market dynamics.
Moreover, recent data shows that the global sustainable packaging market is projected to reach $400 billion by 2027, growing at a CAGR of over 10%. This surge is fueled by innovations such as bio-based materials that reduce carbon footprints and increase recyclability. Companies are also exploring the potential of compostable and biodegradable materials in tray sealing, decreasing reliance on single-use plastics. For example, advancements in tray sealing machinery are enabling manufacturers to implement more efficient and sustainable processes while delivering high-performance products that meet rigorous industry standards.
As the industry moves forward, it is essential for companies to keep pace with these innovations while adhering to sustainability principles. By embracing alternative materials and enhancing tray sealing technology, businesses can not only improve their market positioning but also contribute to a more sustainable future. This synergy between performance and eco-friendliness represents a critical opportunity for growth and innovation within the packaging sector.
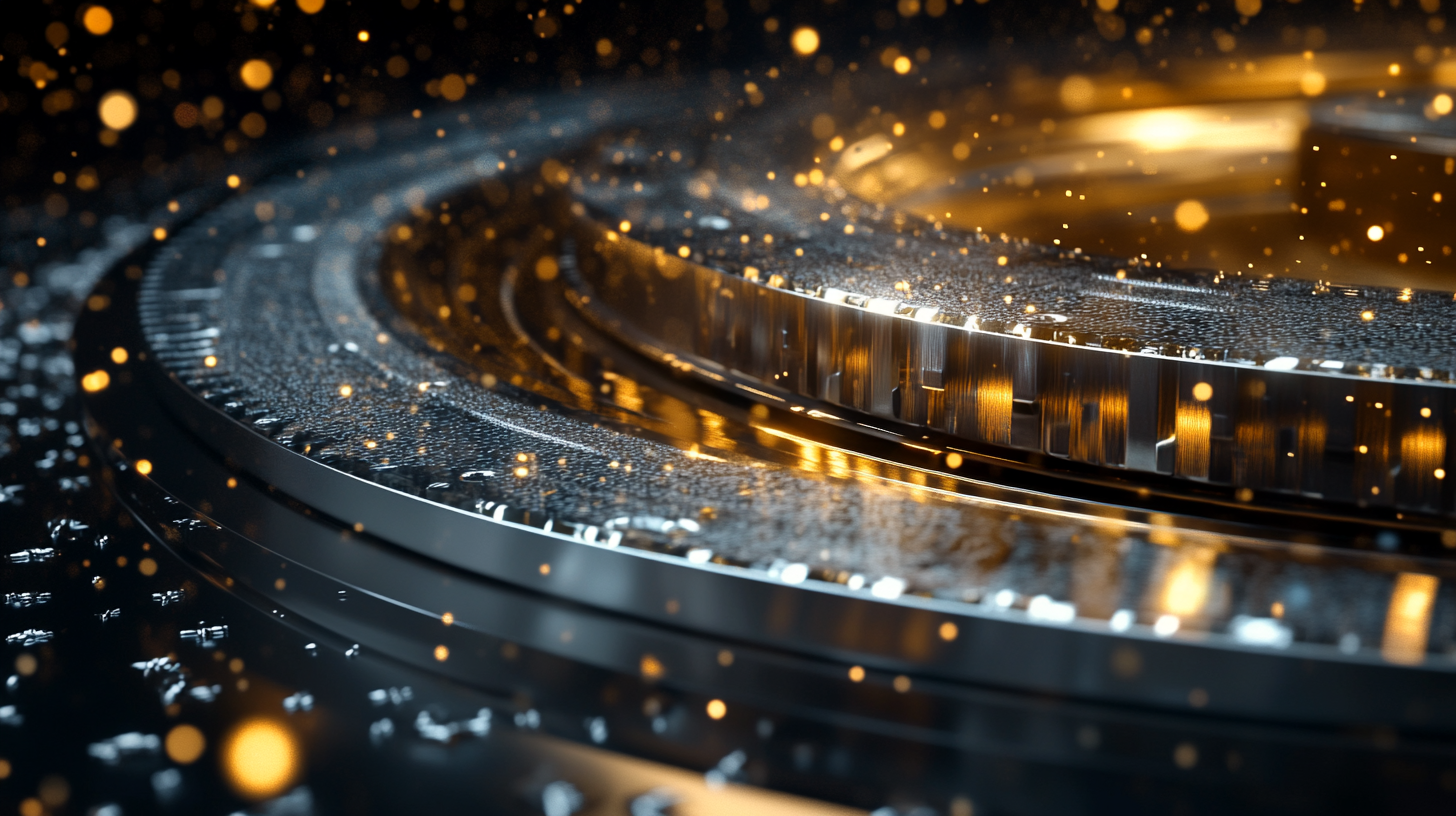
Best Practices for Achieving Consistent Seal Quality in Production
Achieving consistent seal quality in tray sealing technology is paramount for ensuring product integrity and consumer safety. According to a recent report from the Packaging Machinery Manufacturers Institute (PMMI), nearly 70% of food manufacturers cite sealing precision as a critical factor affecting product shelf life and customer satisfaction. To master tray sealing processes, businesses should adopt best practices that leverage advanced technology and rigorous quality control measures.
One innovative approach is the integration of smart sensors into the sealing equipment. These sensors monitor parameters such as temperature, pressure, and seal time in real-time, allowing for immediate adjustments to maintain optimal sealing conditions. Research from the Institute of Packaging Professionals (IOPP) indicates that using this technology can reduce seal defects by up to 40%, leading to fewer product recalls and improved consumer trust.
Another vital practice is the use of standardized sealing materials designed to work seamlessly with specific tray types. As outlined in a recent study by the Food Processing Suppliers Association (FPSA), using incompatible materials can result in seal failures, which are reported to occur in up to 30% of operations that lack rigorous material testing. By selecting the right materials and conducting thorough compatibility tests, manufacturers can enhance seal strength and consistency significantly.
Lastly, continuous staff training is essential for maintaining high-quality standards in tray sealing operations. A study by the National Association of Manufacturers (NAM) shows that companies investing in workforce training see a 20% increase in production efficiency. By educating operators on the nuances of the sealing process and the importance of machine calibration, organizations can foster a culture of quality that leads to consistent, reliable seal performance in their production lines.
Case Studies: Successful Implementations of Advanced Tray Sealing Technologies
The growing demand for eco-friendly packaging solutions has driven innovation in tray sealing technology. Recent case studies highlight successful implementations of these advanced technologies, showcasing how companies are not only improving operational efficiency but also aligning with environmental sustainability goals. For instance, a notable implementation in Wuxi, China, exemplifies the integration of eco-conscious practices within the food packaging industry, demonstrating the feasibility of achieving both performance and environmental standards.
According to the World Packaging Organization, the global market for tray sealing technology is expected to reach USD 4 billion by 2025, with a notable shift towards biodegradable and recyclable materials. This transition is crucial as manufacturers focus on minimizing plastic waste and reducing their carbon footprint. Companies employing advanced tray sealing methods report up to a 30% reduction in material waste, as well as enhanced product freshness, which translates into longer shelf life and lower food spoilage rates.
The British AI Safety Institute is also examining how artificial intelligence can optimize production lines in the food and packaging industries. By harnessing AI algorithms, companies can streamline their tray sealing processes, minimizing errors and increasing throughput. Case studies show that organizations implementing AI-driven solutions in tray sealing can achieve efficiency improvements of over 20%, further enhancing their sustainability initiatives while meeting consumer expectations for higher-quality, eco-friendly products. This multifaceted approach underscores the industry's commitment to innovation and ecological responsibility.